Tras unas semanas de parada, (¿vacaciones?), seguimos con nuestras "queridas" entradas teóricas, en este caso con los sistemas de soldeo, procedamos;
- Clasificación de los métodos de soldeo:
En este caso, os dejo un esquema que explica a la perfección las diferentes clasificaciones y sus métodos. "Una imagen vale más que 1000 palabras, no? ;)".

- Clasificación de los métodos de soldeo:
En este caso, os dejo un esquema que explica a la perfección las diferentes clasificaciones y sus métodos. "Una imagen vale más que 1000 palabras, no? ;)".

-En qué consiste la soldadura y de qué características de los materiales depende.
Se conoce como "soldadura" al procedimiento por el cual dos o más piezas de metal se unen por aplicación de calor, presión, o una combinación de ambos, con o sin aporte de otro metal, llamado metal de aportación, cuya temperatura de fusión es inferior a la de las piezas que han de soldarse.
Soldar consiste en reunir las partes integrantes de una construcción asegurando la continuidad de la materia entre ellas, entendiendo por continuidad no sólo la de carácter geométrico sino la homogeneidad en todo tipo de propiedades.
También se puede considerar soldadura la aportación mediante fusión de material sobre una pieza para modificar las dimensiones iniciales de la misma, o para conseguir características superficiales diferentes a las de origen.
No todos los materiales se sueldan con la misma facilidad, esto es debido a sus características, estas influyen en la manera de unión de dos materiales, es decir, muy difícilmente por no decir de manera imposible, seremos capaces de unir dos materiales diferentes por soldadura.

-Soldadura SMAW

La soldadura manual por arco eléctrico con electrodo revestido es la forma más común de soldadura. Comúnmente la llamamos soldadura por "electrodo".
Mediante una corriente eléctrica (ya sea corriente alterna o corriente continua) se forma un arco eléctrico entre el metal a soldar y el electrodo utilizado, produciendo la fusión de éste y su depósito sobre la unión soldada. Los electrodos suelen ser de acero suave, y están recubiertos con un material fundente que crea una atmósfera protectora que evita la oxidación del metal fundido y favorece la operación de soldeo.
La polaridad de la corriente eléctrica afecta la transferencia de calor a las piezas unidas. Normalmente el polo positivo (+) se conecta al electrodo aunque, para soldar materiales muy delgados, se conecta al electrodo el polo negativo (-) de una fuente de corriente continua.
La posición más favorable para la soldadura es el plano pero se pueden realizar en cualquier posición.
La intensidad y la tensión adecuada para la operación de soldeo se obtiene mediante un transformador. Por medio de diferentes sistemas aplicados al secundario se pueden obtener diversas tensiones, adecuando la potencia del arco al tamaño de las piezas a soldar. Este equipo existe en versiones muy sencillas que permiten realizar pequeños trabajos de bricolaje, es la más habitual en las casas de gente no especializada en la soldadura para pequeñas "chapuzillas".
-Soldadura MIG/MAG


La soldadura MIG/MAG es un proceso de soldadura por arco bajo gas protector con electrodo consumible, el arco se produce mediante un electrodo formado por un hilo continuo y las piezas a unir, quedando este protegido de la atmósfera circundante por un gas inerte (soldadura MIG) o por un gas activo (soldadura MAG).
La soldadura MIG/MAG es mucho más productiva que la soldadura MMA donde se pierde productividad cada vez que se produce una parada para reponer el electrodo consumido.
Este tipo de soldadura tiene un proceso versátil, pudiendo depositar el metal a una gran velocidad y en todas las posiciones, este procedimiento es muy utilizado en espesores pequeños y medios en estructuras de acero y aleaciones de aluminio, especialmente donde se requiere una gran trabajo manual.
La soldadura por gas inerte de metal (MIG) utiliza un electrodo de metal que sirve como material de relleno para la soldadura y se consume durante la soldadura.
El argón es también el gas primario utilizado en la soldadura MIG, a menudo mezclado con dióxido de carbono.
La soldadura MIG fue desarrollada para metales no ferrosos, pero se puede aplicar al acero.


-Soldadura por soplete
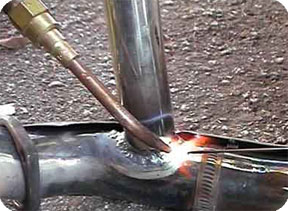
La soldadura del cobre u otros metales con soplete consiste en la unión de partes de cobre con la ayuda de un segundo metal que se funde entre ellas. La temperatura de fusión de la barra del metal de aporte debe ser inferior a la del cobre o metal a soldar. La pieza a soldar no se funde, por tanto no se trata de una soldadura por fusión del material base. Este tipo de soldadura se emplea cuando se quieren unir materiales distintos, o que tienen poca soldabilidad y no se requiere una resistencia alta.
Es la técnica de soldadura más fácil de realizar, incluso por los novatos en bricolaje.
Existen dos tipos de soldadura en lo que se refiere a la temperatura de fusión del material de aporte: la soldadura blanda y la soldadura fuerte.
La soldadura blanda requiere alcanzar temperaturas inferiores a 450ºC, mientras que la soldadura fuerte emplea temperaturas superiores a 450ºC.
Aquí os dejo un vídeo de este tipo de soldadura:
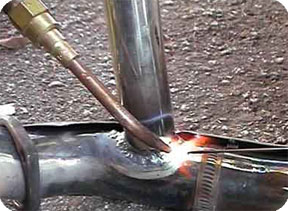
-Soldadura TIG
El proceso de soldadura por arco bajo la protección de gas con electrodo (no consumible), también llamado TIG (Tungsten Inert Gas), usa un arco eléctrico como fuente de energía que se establece entre el electrodo no consumible y la pieza a soldar con la envoltura protectora del gas inerte. Cuando se usa material de relleno, éste se proporciona mediante el uso de varillas, de la misma forma que en la soldadura de oxiacetileno.
Durante el proceso, la antorcha TIG debe estar conectada al polo negativo (-) y la pinza de masa al polo positivo (+).
El proceso TIG se puede utilizar para la soldadura de todos los materiales, incluidos el aluminio el magnesio y los materiales sensibles a la oxidación como el titanio.
Se trata de un proceso mayoritariamente manual con tasa de deposición menor comparado con otros procesos por lo que es utilizado para aplicaciones donde se precisa un acabado visualmente perfecto.
La posibilidad de soldar un material u otro, dependerá de las características del equipo de que dispongamos. El proceso TIG puede utilizarse tanto con corriente continua (DC) como con corriente alterna (AC). La elección de la clase de corriente y polaridad se hará en función del material a soldar.
Aquí os dejo un vídeo que explica a la perfección como soldar con Tig! Espero que os guste y aprendáis mucho.. ;).
-Soldadura por puntos de resistencia
La soldadura por puntos de resistencia se basa en el procedimiento más antiguo que se conoce: la soldadura por forja. Se lleva a cabo aprovechando la propiedad de unión que presentan algunos metales al final de su fase sólida, cuando se aplica sobre ellos una presión.
Para ejecutarla, se eleva el material a temperaturas próximas a la de fusión mediante un calentamiento, y se unen las dos piezas mediante presión. Se trata por tanto de una soldadura por presión y no por fusión.
Éste es el sistema de soldadura que se emplea con mayor frecuencia tanto en fabricación como en reparación, debido a las ventajas que posee frente a otros sistemas de unión:
Siempre que su ejecución se lleve a cabo de la manera correcta, se obtienen soldaduras de buena calidad y uniformes, que presentan una zona fundida homogénea, sin huecos, o grietas...
Siempre que su ejecución se lleve a cabo de la manera correcta, se obtienen soldaduras de buena calidad y uniformes, que presentan una zona fundida homogénea, sin huecos, o grietas...
Su manejo es sencillo, ya que la mayoría de los equipos utilizados hoy en día, tanto en fabricación como en reparación, son automáticos. Por esta razón, la calidad final ya no depende tanto de la destreza del operario, sino de la regulación de los parámetros de la máquina de acuerdo con el tipo de trabajo que se desea realizar.
Ausencia de deformaciones y cambios en la estructura del material, debido a que la aplicación de calor es mínima y se lleva a cabo de forma muy localizada en la zona de contacto de los electrodos.
Las superficies que se obtienen son relativamente suaves, libres de fusión superficial o huellas profundas, que hacen innecesario un repaso posterior como operación de acabado.
No requiere material de aportación, lo cual reduce costes.
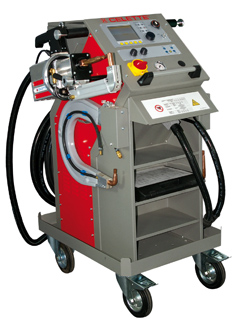
No hay comentarios:
Publicar un comentario